
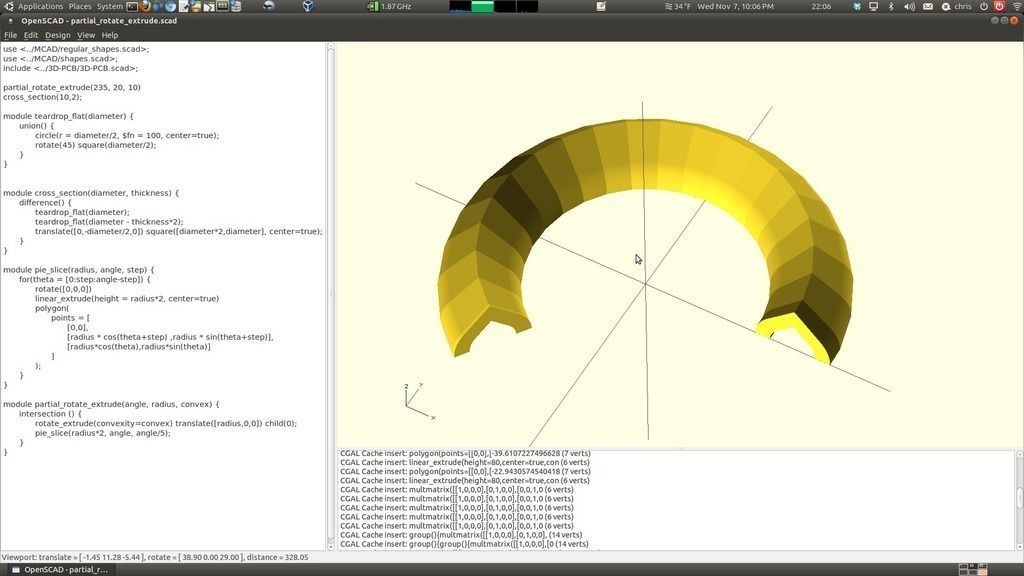
in many extruder designs i saw people putting in "supports" for the tube on the way in and on the way out of the extruder, so that it goes dead-straight both in and out. i have a feeling that many of the problems people have with bowden 1.75mm is due to the thinner tubes, as well as the lack of force that direct-drive extruders can generate. the bowden tube for 3mm is about a 6mm OD, and i like the fact that it's much stronger. Honestly, although it has been a pain, when i convert to 1.75mm i am *not* going to be using the 4mm OD tube. i'll be replacing the MK9 with a MK8 when it arrives in a few days, and i'll do the test again. with a 46:13 (3.54:1) gear ratio on that MK9 drive gear, i can now - amazingly - get 200mm/sec flow in static tests, with 1/4 micro-steps, 225C on the PLA, and 1.2A current - these are 1.8 degrees per step high-torque (84oz-in) motors. That was so pathetic that i decided to create a geared bowden extruder instead. even when ramping the current up to 1.38A (which caused all sorts of other problems), and even when going down to 1/4 micro-steps i was *still* getting skipping. when i made a direct-drive extruder for _that_ combination, it all went horribly pear-shaped very very quickly. Unnnfortunately for me, i got a MK9 drive gear (which is something like 9mm OD!), and i have over 400m of PLA still around from the mendel90. basically they're relying on the thinner diameter (1.75 instead of 3.0mm) reducing the nozzle pressure, as well as having a low-diameter gear (like the MK8 which is really, really low diameter), and that means that you don't need quite such a high torque generated by the motor. The other thing that people tend to do with bowdens is "direct drive". that way you'd actually have the amount of filament coming out that you were actually, genuinely expecting and needing. my take on this is that the correct place to deal with this is in the firmware, to add "PID" to the extrusion fwd/reverse.
#Openscad oval software
gcode software is sort-of solving this by doing relatively-huge, fast retractions of the filament (cura recommends about 4mm). secondly, even if you have it set up correctly, there's quite a bit of "lag". two things about bowdens i don't like: first, you waste about 0.8m of PLA on every single reel (basically the length of the bowden tube). but i did some asking around and some research, first. Now, in the new design (the Sandwich200) i decided to go with a bowden. i had to rack the temperature up to 210C to cope with the speed, which then resulted in jamming (squashing of the filament due to heat travelling up the extruder) - that was solved by running the fan 100% all the time. 100 metres of PLA with it, and the prints are *good quality* at 0.15mm (with a 0.4mm nozzle). a month ago i managed to rack the mendel90 up to 200mm/sec and i've done approximately. I have a mendel90: i really, really like it, and i even didn't notice how loud it was until i did the first prints on the Sandwich200. It looks like the only ones using direct drive are from people who got frustrated with the original bowden design and converted to direct drive afterwards. virtually 100% of them are bowden by design. I am looking at designs here and on openbuilds. That would be a reasonable weight penalty in exchange of not having to deal with very long belts and expensive or low quality pulleys (from my experience all bearings sold at reprap shops have play in them even when new and putting them on an undersized bolt does not make a nice pulley).Įdited 1 time(s). Nema17 weights 400 grams although I think that a smaller and lighter nema motor should be sufficient to drive extruder's carriage. Now with a linear rail X-axis and a bowden extruder you can minimize moving mass to 500 grams but that is still nowhere near to how little mass delta moves.Īnd corexy is just a solidoodle design without a motor sitting on X-axis.
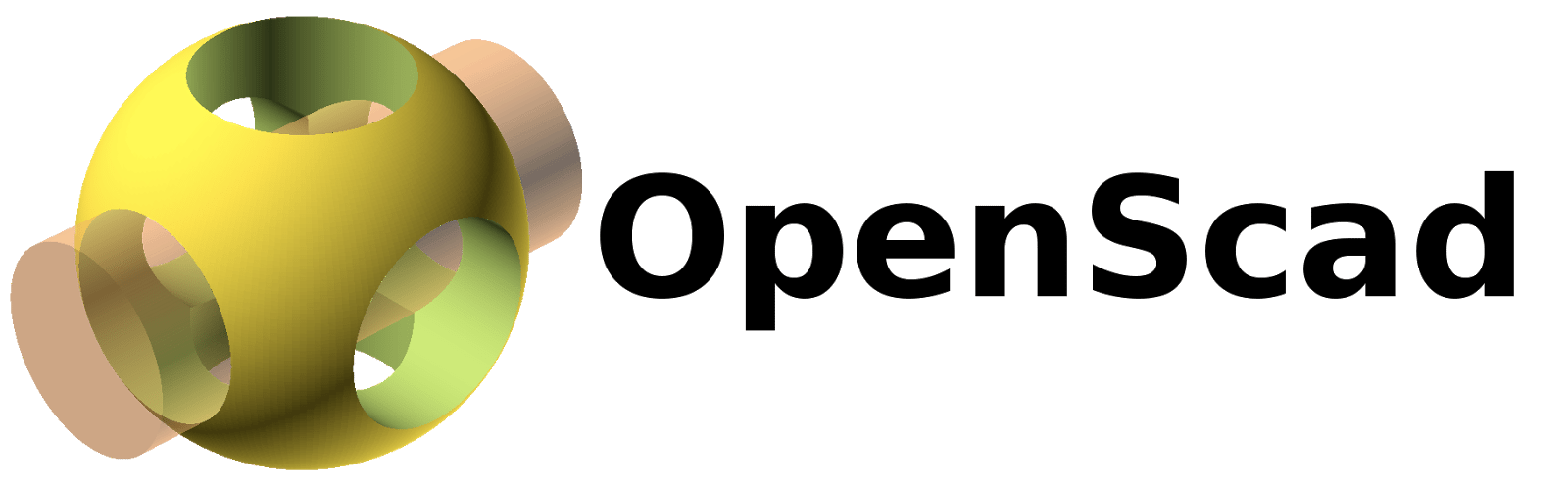
That is a lot of weight to move and it shows in prints although definitely not as bad on a prusa with moving bed.
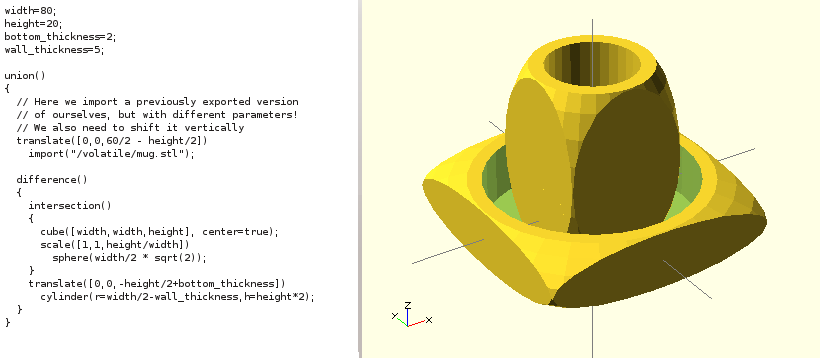
Most of corexy printers have direct drive extruders and corexy has a whole X-axis moving (extruder, linear system of X -axis, bearings of Y axis). It is a hype that corexy is a high speed design. All this mass together with a high speed really shows the direction change on a print. Mine is even heavier and if I print at higher speed I can see circles looking like a hex. He has a heavy direct drive extruder and a cheap smooth rod system. That worked twice.Īlthough I think I know what he is talking about. I tensioned belts to where they are neither too tight nor too loose and did not feel a need to do any further adjustments.
